Fitzbionics is a team of world-class design engineers and manufacturers who conceive, design, develop, manufacture, and implement new implants for the patients of Fitzpatrick Referrals.
The team is based in Hemel Hempstead where they design and manufacture on-site, communicating with the team at Fitzpatrick Referrals to create standard and custom-made implants for patients in need of a solution, which do not exist anywhere in the world.

Bioengineering excellence
How we work together
Fitzpatrick Referrals and Fitzbionics work closely together to develop and deliver implants and surgical equipment for our patients.
Meeting the need
The team at Fitzpatrick Referrals get in touch with Fitzbionics detailing the clinical problem that needs addressing, the affected limb, joint or area with patient details such as breed, weight and height along with the urgency.
Making a plan
Using the knowledge of what sort of implant is needed and the availability of design and manufacturing engineers, the team let the surgeon know an approximate delivery date of the implant so the surgery can be booked in.
The team use patient CT scans to identify whether a stock item or customised design is required. If stock items are not suitable, the engineer and surgeon will work on a design to create a suitable implant, surgical instruments, and guide system for the individual case.
Setting a delivery date
Once both the surgeon and engineer are happy with the design, a timeframe and cost can be determined for the manufacture and completion of the implant, which is shared with the family.
If the need of the patient is unique and has not been done before, the delivery date and manufacture time can take longer as it is developed.
Manufacturing
Once approved by the family, and the design has been finalised, the design team discuss with the manufacturing engineers how long they need for manufacturing and check there is enough material in stock to confirm a delivery date.
The design team share with manufacturing the design drawings, detailing the dimensions and exact hole positions for attaching the implant. They will use 3D printers, CNC (computer numerical control) machines, manual milling machines and lathes where necessary to make the part to specification.
Final implant is created
Once the implant has been created, it is assembled to ensure all components fit together, if there are multiple components. When the team is happy with the final implant, it is polished to the desired finish on the polishing wheel and then cleaned and packaged up before being couriered to the practice for surgery.
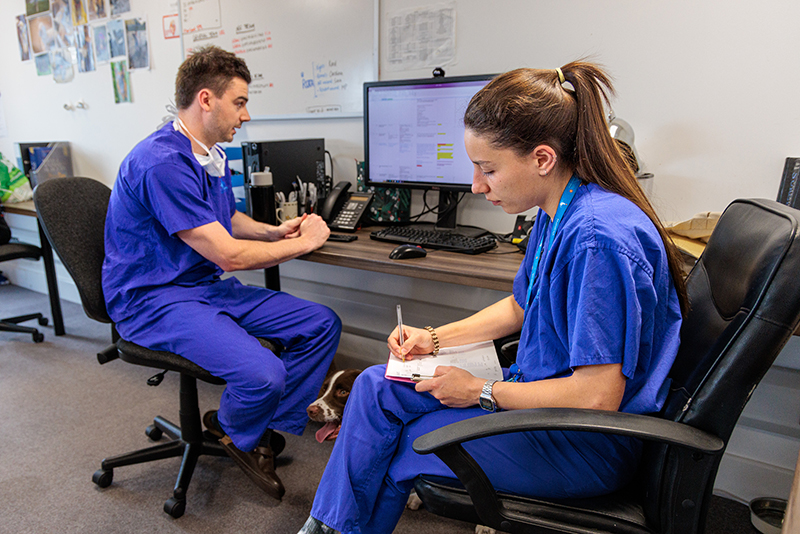
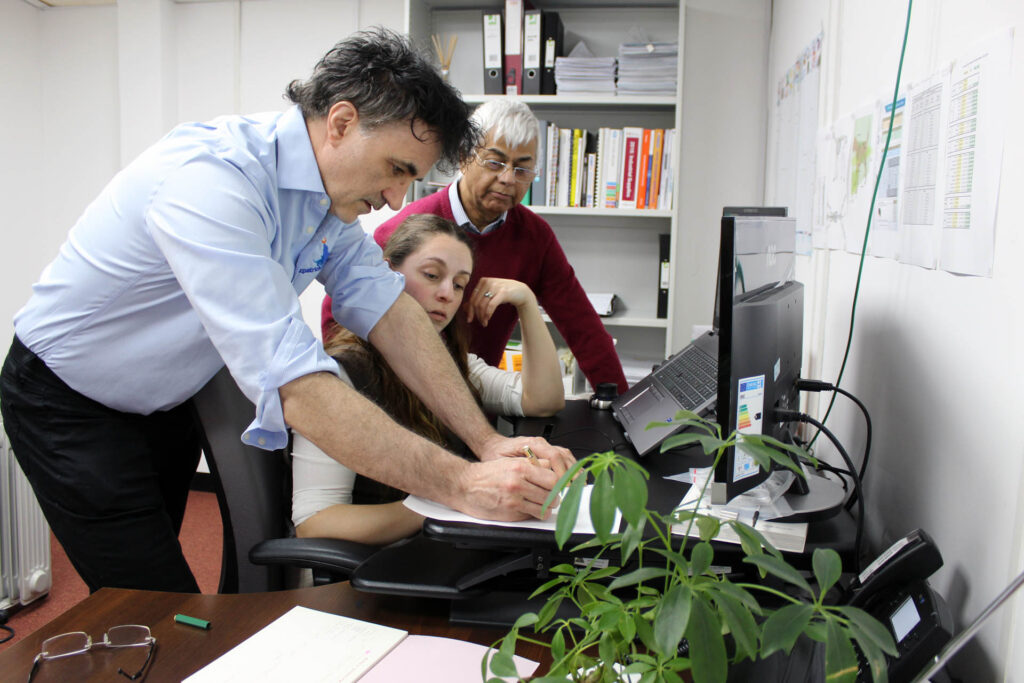
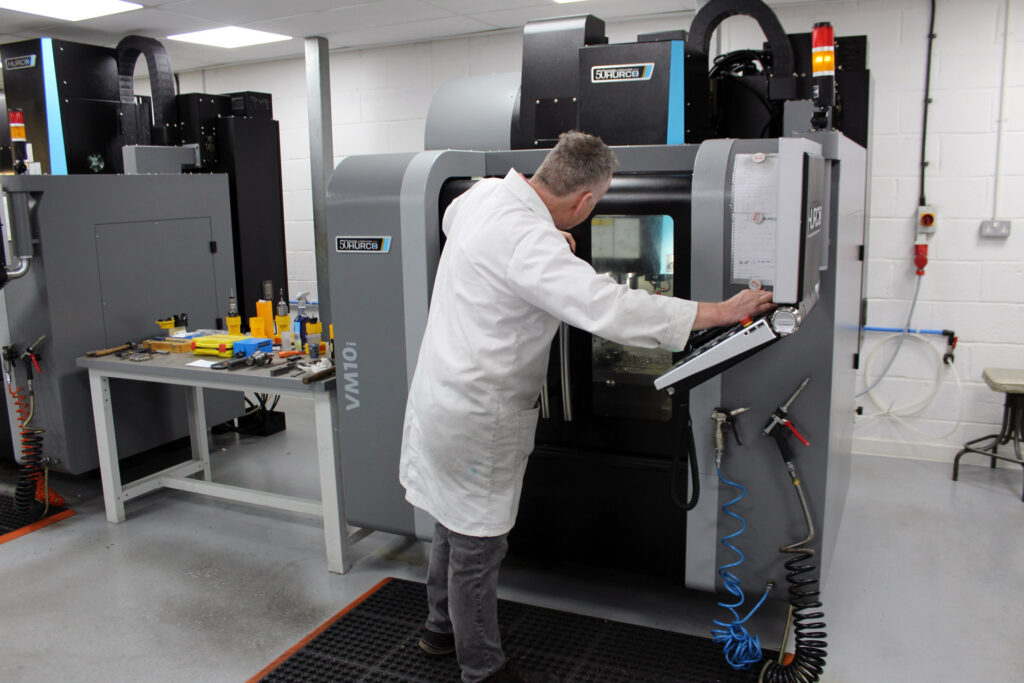
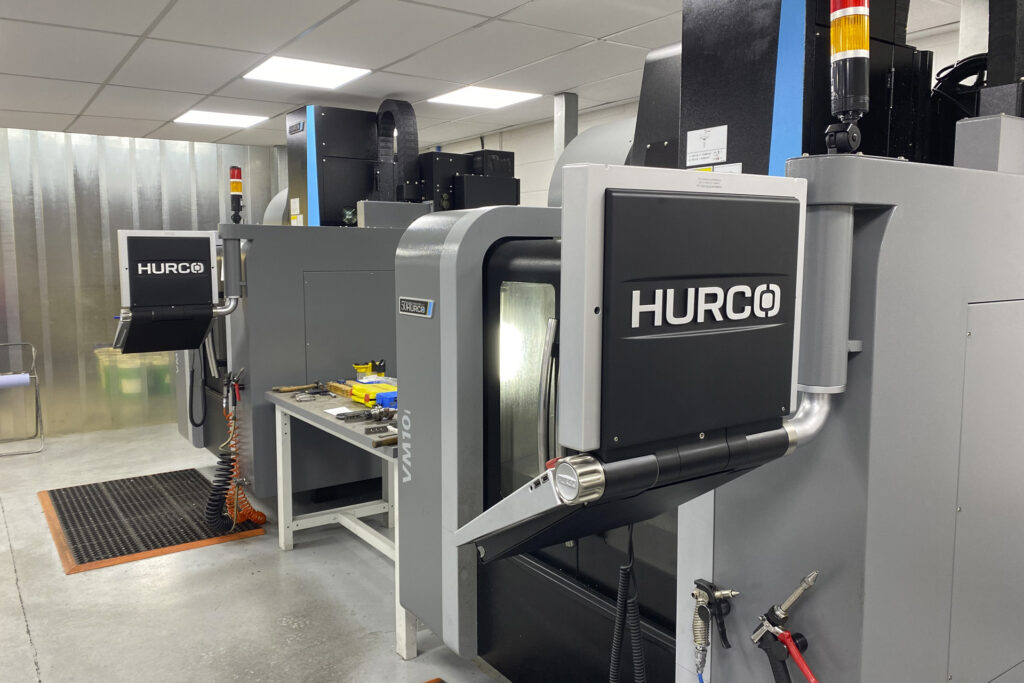
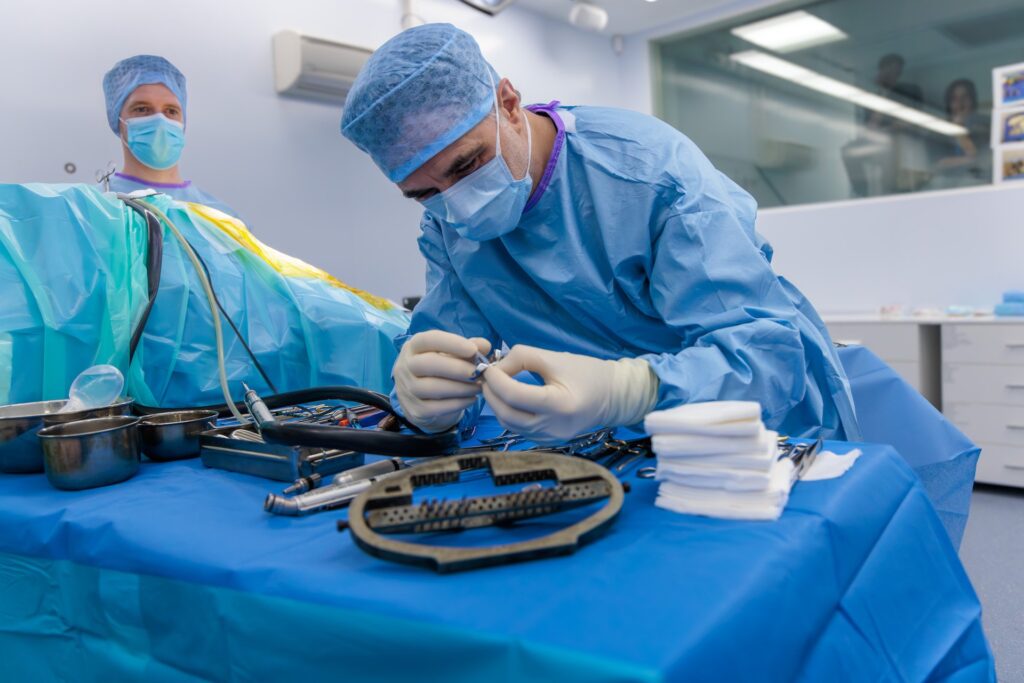